Lubrication Program Development
You work hard to keep your equipment running.
But what if your lubrication program is setting you up for failure?
If you’re like most maintenance or reliability professionals, you think your lubrication program is in decent shape until a critical failure proves otherwise.
Take the FREE Self-Assessment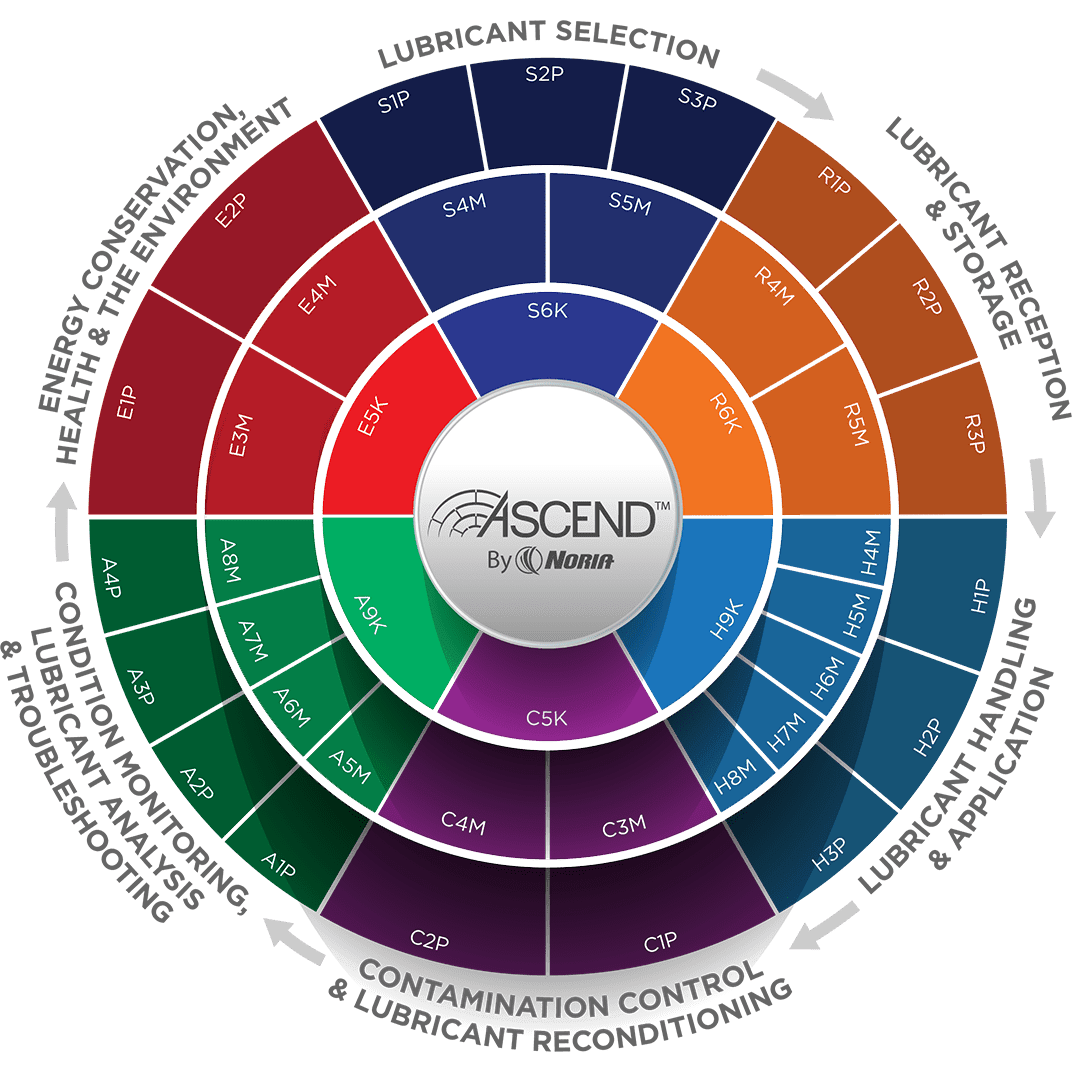
The Hidden Weakness in Your Reliability Strategy
Most plants don’t have a lubrication program — they have bad habits.
Without a structured program, lubrication becomes a hidden liability, not the reliability driver it should be. Those habits are often undocumented, inconsistent, and reactive.
You are probably:
- Over/under greasing without knowing it
- Mixing incompatible lubricants
- Relying on tribal knowledge instead of standard procedures
- Missing lube points
Your 3-phase plan to gain confidence in every lubrication decision.
-
Phase 1: Ascend Assessment
Our 543-point assessment includes a benchmark of your current lubrication practices, a customized roadmap to success, and a detailed report to help you cost-justify improvements.
-
Phase 2: Engineering Design
Next, we build your lubrication program from the ground up. This includes creating standard procedures, calculating proper volumes and frequencies, and providing lubricant and hardware recommendations based on your equipment and goals.
-
Phase 3: Program Implementation
Finally, we help you turn that design into a working reality. From training your team to designing lube routes in our proprietary Lubrication Management Software, we stay by your side to make sure your program delivers lasting results.
Success Stories
Case studies from our customers
Learn how you can drive success with lubrication
Lubrication & Contamination Done Right from the Start
at Blue Buffalo
When Blue Buffalo called Noria, they were in the process of designing and building their 450,000-square-foot Richmond plant. Before machines were installed, they worked with Noria to ensure that the right inspections, contamination control activities and lubrication procedures would be in place from day one. Over the course of a year, Noria visited the plant six times to identify lubrication points, document procedures and train staff. The plant was subsequently the recipient of the 2021 John R. Battle Award for lubrication excellence, showcasing its dedication to best practices and continuous improvement.
Lubrication program enables Simmons Feed to cut downtime by 50%
The Simmons Feed Ingredients plant in Southwest City, Missouri, brought in Noria consultants to develop a road map for lubrication excellence. After implementing Noria’s Lubrication Program Development and training, the facility was able to achieve cleaner oil, prevent machine failures, avoid lost production and save up to $1 million a year.
Hardware creates culture change at Argos Newberry
The Argos Cement Plant in Newberry, Florida, had a directive from their corporate team to improve lubrication procedures and hardware but needed help getting started. After receiving Noria training and an Ascend Assessment, the plant was able to work with the Noria team to identify better lubricant handling options, more effective greasing techniques and opportunities for better contaminant exclusion and removal. Their success has encouraged the Argos team to implement similar improvements in their other plants as well.
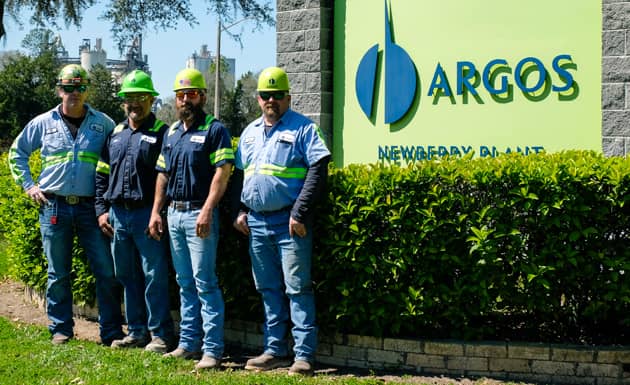
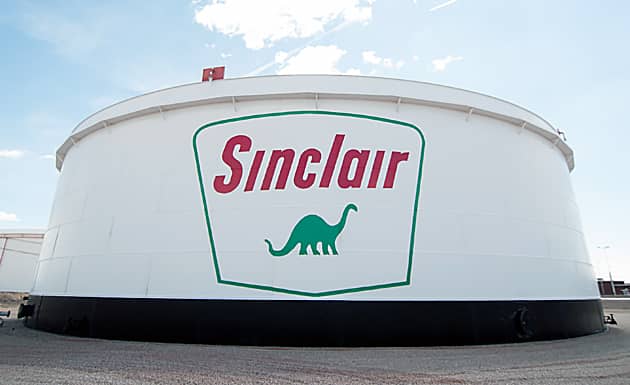
Proactive maintenance approach at Sinclair impacts bottom line
Noria’s onsite training and Lubrication Program Development helped transform the Sinclair Wyoming Refinery into an industry leader for machinery lubrication. With guidance from Noria, the refinery was able to shift to a proactive maintenance approach and adopt best practices, significantly impacting its operations and bottom line.
Contact a Noria expert today
Frequently asked questions
Who can benefit from LPD?
Anyone who makes decisions about lubrication in their worksite, plant or facility can lead a lubrication program development effort. Noria experts will be with you every step of the way to answer questions and provide recommendations for success.
How long is the process?
Lubrication Program Development (LPD) is divided into three phases, each one is listed with its average timeline below:
Phase I: Ascend Assessment
1 week
Phase II: Engineering Design
6 – 8 weeks
Phase III: Implementation
1 – 2 years